Instructions
This memo describes material-modeling support for PFC 9.0 as provided in the PFC FISHTank (or fistPkg), and this memo corresponds with fistPkg9.2.
The following capabilities are provided by fistPkg9.2:
- Material genesis of linear, contact-bonded, parallel-bonded, soft-bonded, flat-jointed and
user-defined (3D hill) materials in polyaxial, cylindrical and spherical physical vessels or
polyaxial periodic vessel. Material grains can be balls or clumps, and 3D flat-jointed
materials of spherical, Voronoi or tetrahedral grains. Stress can be installed into the finalized
periodic ensemble (after bonding), and then this ensemble can be converted into a periodic
brick which is assembled into a larger geometric shape. Material tests are compression
(confined, unconfined and uniaxial strain), diametral-compression and direct-tension.
Microstructural monitoring includes properties (such as grain-size distribution) with
microstructural plot sets and crack monitoring for bonded materials.
Usage instructions are given in fistPkg-README.txt and summarized as:
- Create a 2D or 3D material (using the appropriate MatGen project).
- Perform compression, diametral-compression and direct-tension tests on the material (usingthe CompTest, DiamCompTest and TenTest projects).
Download Files
PFC 9.0
Material-Modeling Support Package, fistPkg9.2 (ZIP, 96 MB)
Material Modeling Support 9.2 (PDF, 13.9 MB)
Material Modeling Support 9.2, Materials 1 (PDF, 5.3 MB)
Material Modeling Support 9.2, Materials 2 (PDF, 4.4 MB)
Material Modeling Support 9.2, Materials 3 (PDF, 1.3 MB)
Material Modeling Support 9.2 Updated Webinar (PDF, 10.7 MB)
PFC 7.0
Material-Modeling Support Package, fistPkg7.4 (ZIP, 149 MB)
Material-Modeling Support Package, fistPkg7.3 (ZIP, 138 MB)
Material Modeling Support 7.3 (PDF, 16 MB)
Material Modeling Support 7.3, Materials 1 (PDF, 20 MB)
Material Modeling Support 7.3, Materials 2 (PDF, 6 MB)
Material Modeling Support 7.3, Materials 3 (PDF, 3 MB)
Material Modeling Support 7.3 Updated Webinar (PDF, 44 MB)
PFC 6.0
Material-Modeling Support Package, fistPkg6.6 (ZIP, 87 MB)
Material Modeling Support 6.6 (PDF, 16 MB)
Material Modeling Support 6.6, Materials 1 (PDF, 16 MB)
Material Modeling Support 6.6, Materials 2 (PDF, 6 MB)
Material Modeling Support 6.6, Materials 3 (PDF, 3 MB)
Material Modeling Support 6.6 Updated Webinar (PDF, 37 MB)
PFC 5.0
Material-Modeling Support Package, fistPkg26 (ZIP, 74 MB)
Material-Modeling Support Update Revisions
The first column of this table lists the fistPkg revision number; the second column lists the PFC release against which the fistPkg has been tested; and the third column describes the fistPkg revision. Note that each revision of the fistPkg is expected to operate with a PFC release that is current or newer than that listed. Since newer revisions of the fistPkg may use features available only in newer revisions of PFC, they may not be compatible with older revisions of PFC.
fistPkg Release | PFC Release | Date / Description |
---|---|---|
9.2 | 9.00.177 |
|
9.2a | 9.00.173 |
|
9.1 | 9.00.162 |
|
7.4 | 7.00.161 |
|
7.3 | 7.00.159 |
|
7.2 | 7.00.137 |
|
7.1 | 7.00.132 |
|
6.6 | 6.00.17 |
|
6.5 | 6.00.11 |
|
6.4 | 6.00.8 |
|
6.3 | 6.00.8 |
|
6.2 | 6.00.7 |
|
6.1 | 6.00.02 |
|
26 | 5.00.35 |
Bug Fixes:
Enhancements:
|
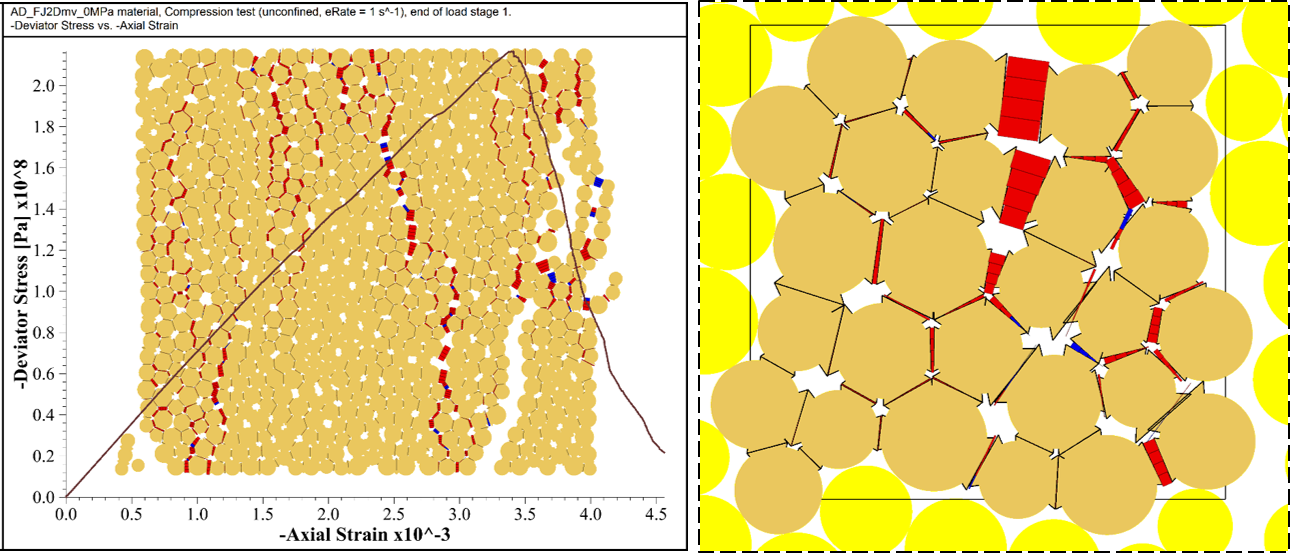
25 | 5.00.35 |
5/3/2018 Consistency test against PFC 5.00.35 successful |
25 |
5.00.30 |
3/20/17 Enhancements.
|
24 | 5.00.30 |
2/28/17 Consistency test against PFC 5.00.30 successful. |
24 | 5.00.29 |
1/18/17 Consistency test against PFC 5.00.29 successful. |
24 | 5.00.27 |
10/12/16 Enhancements.
|
23 |
5.00.24 |
06/23/16 Enhancements.
myMatGen-X ==> MatGen-X, where |
22 | 5.00.24 |
05/16/16 Enhancements.
|
21 | 5.00.23 |
04/18/16 Enhancements.
|
20 | 5.00.23 |
02/26/16 Enhancements.
REFERENCES: |
19 | 5.00.22 | 01/12/16 Create microstructural plot sets --- see Section 3.2 {Microstructural Plots}. Hide many of the views, they are manipulated via the Documents button. Modify default values of _mvMpFacH and _mvMpFacW from 0.9 to 0.8; these values control the size of the measurement spheres used to measure stress and strain in the material. |
18 | 5.00.22 |
12/10/15 Enhancements.
|
17 | 5.00.21 | 09/22/15 Enhancements.
|
16 | 5.00.20 |
07/22/15
|
15 | 5.00.17 | 04/22/15 Add capability to create a user-defined material, with a user-defined material example that creates a 3D Hill material. |
14 | 5.00.15 | 02/17/15 Add diametral-compression test for PFC2D, with usage example for the 2D parallel-bonded material. |
13 | 5.00.15 | 02/05/15 Remove the packing parameters: pk_emod and pk_krat. These two properties are replaced by the properties of either the linear material group (lnm_emod and lnm_krat) or the user-defined contact model (as specified in the udm_setMatBehavior FISH function). |
12 | 5.00.15 | 02/02/15 Two enhancements: (1) Add a spherical material vessel. (2) Add diametral-compression test for PFC3D, with usage example for the parallel-bonded material. Break the material-modeling support memo into three related memos named "Material-Modeling Support in PFC," and "Material-Modeling Support in PFC (Example Materials {1,2}." |
11 | 5.00.15 | 01/27/15 Two modifications: (1) Fix bug in computation of servomechanism gain in axial direction for 3D cylindrical vessel, and improve computation of wall-based stresses (now controlled by mv_wAreaMode). (2) Add Potyondy (2014) to documentation directory (see reference in entry for fistPkg 10). |
10 | 5.00.15 | 01/20/15 Modify "Material-Modeling Support in PFC" memo to correspond with updated PFC 5.00.15 documentation set, and to refer to Potyondy (2014). Enhance compression test to support fully unconfined tests. [REFERENCE: Potyondy, D.O. (2014) "The Bonded-Particle Model as a Tool for Rock Mechanics Research and Application: Current Trends and Future Directions," Geosystem Engineering, 17(6), 342-369.] |
09 | 5.00.14 | 11/17/14 PFC 5.0 FISHTank released to users as fistPkg09. |
08 | 5.00.14 | 10/20/14 Update the PowerPoint slide set that summarizes Potyondy (2014a). REFERENCE: {Potyondy, D. (2014a) "Material-Modeling Support in PFC," Itasca Consulting Group, Inc., Minneapolis, MN, Technical Memorandum ICG7766-L, October 20, 2014.} |
07 | 5.00.9 | 10/10/14 Initial release of the PFC 5.0 FISHTank, which provides the following capabilities (for both PFC2D and PFC3D): material genesis of linear, contact-bonded, parallel-bonded and flat-jointed materials (all grains are balls) in physical material vessels (cylindrical and polyaxial) with compression and direct-tension testing. |
06 | 5.00.9 | 09/19/14 Minor enhancements since fistPkg05. fistPkg06 has been released for selective internal Itasca review. |
05 | 5.00.9 | 09/04/14 Material genesis of linear, contact-bonded, parallel-bonded and flat-jointed materials in physical material vessel with compression and direct-tension testing (PFC3D only, all grains are balls). Not yet available: (1) extend to support PFC2D, (2) allow grains to be clumps, (3) provide Brazilian-tension and fracture-toughness tests, (4) provide smooth-jointed interface and (5) provide stress-installation procedure. |
04a | 5.00.9 | 07/25/14 THIS IS A PRIVATE VERSION of ongoing developments, created for use of Derrick Blanksma. It supports creation of a linear material, and compression testing of that material. Note that it has been tested with PFC 5.00.9, it should probably work with more recent versions of PFC as well. |
03 | 5.00.9 | 06/25/14 Modified interface to compression-test procedure to make it correspond with description in the memo: "Material-Modeling Support in PFC." |
02 | 5.00.9 | 06/22/14 Material genesis and compression testing can be performed on the linear material for which all grains are balls. |
01 | 5.00.7 | 06/10/14 Establish initial tank to support creation of linear material and compression testing (PFC3D only). |